Metal coating process
1, coating method
A single printed tinplate can be processed into three food cans, beverage cans and spray can containers. Depending on the characteristics of the substrate and the purpose of use, it should have appropriate corrosion resistance and printing and processing properties. For this purpose, the undercoating should be carried out before printing. Printing-related coating processes mainly include pre-press coating, surface white coating, side seam coating, and glazing (post-press coating).
Prepress coating: Coating with a primer. The coated surface should be degreased prior to coating to remove oil from the surface. The prepress is coated with both inner and outer coatings. The inner coating is applied inside the iron sheet, that is, the inner side of the molded product, and a layer of protective varnish is applied to protect the iron sheet from the etch of the contents, and at the same time protect the contents. Since the inner coating is directly in contact with the food, the coating is required to be non-toxic and odorless, and should be dried in a desiccator after the inner coating. The outer coating is to coat the printing surface, and its function is to improve the adhesion between the metal surface and the ink layer. Therefore, the coating is required to have a strong bonding force to the metal surface and also has a good affinity for the ink layer, which requires the coating itself to have good fluidity, water resistance and color rendering.
White coating: The metal surface is coated with a white paint or a colorless clear paint. Often used as the base color for printing full-page graphics. The white paint should have good adhesion and whiteness, and it will not yellow or fade under high temperature baking conditions, and will not fall off or peel off during the can making process.
Side seam coating: refers to a coating method in which the resistance welding can is used to fill the can seam with the edge seam coating to prevent corrosion.
Post-press coating (glazing): Apply a layer of varnish on the surface where all the graphic printing has been completed. The purpose is to increase the gloss of the printing surface, protect the printing surface, and improve the light resistance and chemical resistance of the metal surface. .
2, coating machine
The coater is used as a separate metal printing auxiliary machine, and is also equipped with a feeding mechanism and a conveying mechanism as well as a tunnel oven. The automatic feed mechanism is similar to the metal press feed. Before entering the drum, the tinplate needs to adjust the position of the push plate and the belt mechanism, and basically position it to prevent the sheet from skewing. If the chain is too loose, too tight or the two sides of the push head are inconsistent during operation, the sprocket center distance can be adjusted.
There are three types of rubber rolls commonly used in coating equipment: the first type uses a thick blanket, that is, a solvent-resistant blanket of about 5 mm thickness is wrapped on a hollow iron roll. This type of rubber roller has good coating quality and is suitable for full-page printing. The second type is wrapped in a rubber pad felt on an iron roll, which is suitable for full-coating of general products. The third type is a rubber roller that is grooved according to the image area, and is mainly used for resistance welding products such as food cans and aerosol cans.
The role of the scraper in the coating device is to scrape the paint off to avoid stripping the back of the sheet.
3. Coating process
The paint in the oil pan is pumped by the gear pump to the lower oil transfer roller, and the lower oil transfer roller is meshed with the transfer oil roller gear, and is relatively rolled in the radial direction and the axial direction, and then the paint is applied to the rubber roller. on. In order to control the amount of paint flow, the pipeline is provided with a safety valve adjustment mechanism. The adjustment of the oil transfer roller is very important for the thickness and uniform distribution of the paint, which directly affects the quality of the product. The adjustment is required to be the same as the axis (center line) of each roller and the contact pressure (ie, the gap). The gap size of the upper and lower oil transfer rolls needs to be adjusted according to the requirements of different product coating thicknesses. When the pressure of the oil roller and the rubber roller is adjusted, the steel sheet is inserted and pulled, and the tension is appropriate. The adjustment of the rubber roller is also carried out according to the thickness of the tinplate. Coating requires uniform coating on the same sheet, and the coating amount of each batch is consistent.
Wing Kam Packaging Co.,Ltd. was established in 2001, we are manufacturer and support custom design. We specialize in this Foldable Box Packaging. Our value message is "QUALITY IS OUR LIVE, WITHOUT QUALITY, WITHOUT US." If you order this Foldable Box Packaging from us, YOUR BUSINESS WILL BE SAFE, YOUR MONEY WILL BE SAFE, YOUR PRODUCT OUT LOOK WILL BE GORGEOUS.We also provide flower plastic container.
Item |
Foldable Box Packaging |
Dimension |
Customized |
Material |
PVC, PET |
Thickness |
0.2mm to 1mm |
Cardboard Insert |
Yes, Customized |
MOQ |
3000pcs |
Sample order |
Welcome & acceptable |
Product Pictures Show:
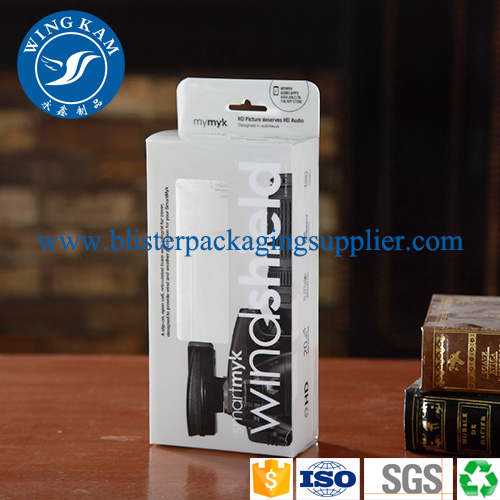
Welcome to order Foldable Box Packaging.
Any questions please contact us freely.
Foldable Box Packaging
Triangle Foldable Boxes Packaging,Plastic Foldable Box Packaging,Magnetic Foldable Paper Packaging Box,Cardboard Foldable Box Packaging
Shenzhen City Wing Kam Packaging Products Co., Ltd. , https://www.blisterpackagingsupplier.com