Upper edition
First, proofread the die-cut version that has been made, and roughly observe whether it meets the requirements of the design draft. Whether the position of the steel wire (crimping knife) and steel knife (die cutter) is accurate; whether the incision of the slotted hole adopts the complete line, and whether the line turns at the corner; for the sake of facilitating the elimination, adjacent narrow edge waste Whether the connection has increased the connection part and connected them together; whether there are sharp angles at the joints of the two lines; whether there is a case where the sharp line ends at the middle of another straight line. Once the above issues arise in the die-cut version, the plate-making personnel should be notified immediately to make corrections to avoid more time wastage. Then, the prepared die-cut version is installed and fixed in the plate of the die-cutting machine, and the position of the good version is initially adjusted.
Adjust pressure, determine rules and paste rubber plugs
Adjust the layout pressure, first adjust the pressure of the steel knife. After padding, first press the print several times to flatten the steel knife, and then use a cardboard larger than the die-cut layout to test the pressure. According to the marks cut by the steel knife on the paper board, gradually increase the pressure by using the partial or all. The method of reducing the number of backing paper layers makes the pressure of each cutting line of the layout uniform. In general, the steel wire is 0.8mm lower than the knife line (because the corrugated paperboard has different types of corrugated paperboard, the thickness of the paperboard has a large gap and should be adjusted according to the actual situation). To make the steel wire and steel knife get the ideal pressure, it should be based on the die-cut cardboard. The nature of the adjustment of the pressure on the steel wire. The thickness of the liner is usually calculated based on the thickness of the die-cut cardboard, ie, the thickness of the liner = the height of the steel blade - the height of the steel wire - the thickness of the cardboard being die-cut.
Remark: After the plate pressure is adjusted, fix the die plate. When determining the position of the rule, it is generally best to center the die-cut product. The rubber plug should be placed on the two sides of the main steel knife of the die-cutting plate, and the separated cardboard should be pushed out from the edge using the good recoverability of the rubber elastic bar. Generally speaking, the rubber band should be about 1.2mm higher than the cutting edge, and the distance from the rubber line to the cutting line should be 1mm to 2mm, because if it is only installed by the blade, the rubber cannon cannot expand in the direction of the blade after being pressed. Can be inflated in the other direction, causing the paper to be pulled on both sides. The die cutter has not cut the paper and has been broken by the rubber stopper. It is easy to produce paper.
Pressure Die Cutting, Formal Die Cutting, Stripping, Finished Product Inspection, Point Packaging
After the above work is completed, proofs should be die-cut first, and a comprehensive inspection should be conducted to see if the indicators meet the requirements. After the full-time inspection personnel confirms the sample, mass production can be carried out. During the production process, operators should perform self-tests from time to time. It mainly compares with sample proofs to see if there are any problems and solve them in time. For die-cut products, excess edge material should be removed, and the burr edges should be polished to make it smooth and free from burrs. Afterwards, the finished product was selected for inspection, defective products were removed, and the final number, packaging, acceptance, and storage were completed. Equipment characteristics and development trends The equipment used for die-cutting and indentation processing is called die-cutting machine. According to the different shapes of the main working parts of die-cutting plate and die-cutting structure, there are three types of die-cutting machines commonly used in the market: Flat-pressing flat type Die-cutting machine, flat-pressing circular die-cutting machine and round-pressing circular die-cutting machine. However, no matter which type of die-cutting machine, the structure is composed of die-cutting table and press-cutting mechanism. Here's a brief look at how they work and their advantages and disadvantages:
Flat-press die cutting machine
Working principle: The die-cutting platen and the press-cutting mechanism of the flat-pressing die-cutting machine are flat-shaped. The die plate is fixed on a flat plate table, and the processed sheet is placed on a press plate (press plate). During the work, the die-cutting platen is fixed and the pressure plate reciprocates through the crankshaft connecting rod, so that the platen and the pressure plate are continuously separated and pressed, and once each combined pressure, a die-cut is realized. Common flat and flat die-cutting machines include vertical die cutters and horizontal die cutters. At present, the vertical die-cutting machine is mainly converted from a flat-pressing type printing press; and the horizontal die-cutting machine is similar to the single-color offset printing press in that it has a feeding section, a molding section, and a discharging section, and some have Automatic stripping device and other components.
Advantages and Disadvantages: Due to its advantages of simple structure, easy maintenance, easy operation, easy replacement of die-cutting indentation plate, suitable for different grammage materials, accurate die-cutting, etc. So it has a wide market. However, its inadequacies are also obvious. For example, it needs a great deal of pressure to work, resulting in labor intensity and low productivity. It has a wide range of applications and is suitable for die-cutting and indentation processing of folding cartons, pasting cartons, and corrugated cartons. It is currently a relatively common die-cutting equipment for domestic use. The continuous feed automatic die cutting machines produced in Tangshan Yuyin in China are the most popular.
Round flat die cutting machine
Working principle: The working principle of the round-press flat die-cutting machine is similar to Heidelberg's early round-flattening type printing press. Its die-cutting platen is flat, the die-cut plate is fixed on its upper surface, and the die-cutting platen can be With the help of the pulley on the back, it moves back and forth, and the processing sheet passes through the gripper of the embossing cylinder. During work, the platen moves forward as the embossing cylinder is running, thereby achieving die cutting. Before the gripper continues to pick up the next piece of paper, the platen moves back to the starting position (at this time The table is not in contact with the working surface of the mold roller, which is convenient for the next die cutting work.
Advantages and Disadvantages: Most of these die-cutting machines were transformed from early Heidelberg round-pressing presses. The device uses a cylindrical pressure roller instead of the platen, so the work is not "surface contact" but "line contact" The machine requires less pressure when die-cutting, so the load of the machine is relatively stable. However, due to the component force generated when the die-cut plate and the embossing cylinder roll on each other, it easily leads to deformation and displacement of the knife line, and its application range is relatively narrow, generally only suitable for die-cutting of cardboard with a grammage less than 400 g/m2, particularly suitable for Paper die cutting and electro-aluminum foil bronzing. In the paper cutting process, attention should be paid to the fiber direction of the paper, generally it should be parallel to the axial direction of the molding roller, otherwise it will cause serious paper stretching phenomenon.
Round press die cutting machine
Working principle: The shape of the working part of the die cutting table and the pressure cutting mechanism (pressure roller) of the circular press die cutting machine is cylindrical, and the principle of molding is similar to the offset printing press. A semi-circular die plate (or metal die-cutting roll) with the same or two arcs as the die platen substrate (ie, die-cutting platen cylinder) is fixed on the die-cutting plate cylinder, and the pressure roller surface is coated with a layer Protect the cutting edge of polyester plastic. As the molding process progresses, the surface layer of polyester plastic will be destroyed. Therefore, the polyester plastic on the surface layer is generally removed from time to time to replace the new plastic layer. During molding, the feed roller feeds the processed sheet material between the die-cutting plate cylinder and the pressure roller, both of which sandwich the roller platen and press it. The die-cut platen roller completes a die-cutting task after one rotation.
Advantages and Disadvantages: Because the drum is continuously operated when the die cutter is working, its working efficiency is the highest compared to other die cutters. It is particularly suitable for mass production, but it is precisely because of its fast die cutting speed. As a result, sometimes the required die-cutting accuracy cannot be guaranteed. Like the round flat die cutting machine, it adopts the line contact principle to complete the molding work. Therefore, when the die cutting requires less pressure and the pressure distribution is relatively uniform, the load of the machine is relatively stable. However, its die-cut version is bent into a curved surface, so it is cumbersome in the plate-making and loading process, the technical difficulty is relatively large, and the plate-making cost is also relatively high. The die-cutting plate required for the round-pressing rotary die-cutting apparatus is flatter than flat. The cost of die cuts is 25% to 100% higher.
Circular press die cutting machine is mainly used for die cutting of corrugated products. The current market share is very low. However, with the advancement of science and technology, the development trend of the die cutting machine is better, because it adapts to the requirements of the future mechanization, linkage and automation of the postpress processing, and people can link the molding mechanism and the printing machine as required. The production line realizes the online operation, which can effectively reduce the demand for labor, shorten the process flow and reduce the loss in the process, thereby increasing production efficiency, reducing labor costs, and obtaining greater profits.
Elegant gifts, YYX bag accessories add a marvelous finishing touch to a look, echoing the unique spirit of your brand. Offered in many versions, in shiny gold or silver, they are both useful and fun, giving you the opportunity to personalise bags fabulously.
Create unique custom bag accessories for your company or brand with your choice of the overall shape, size, colors, materials and finishes. YYX Company also offers the option of creating your pendants or charms out of precious metals for special occasions when you want to give everyone, something that will last forever. We can fulfill orders as small as 1000 pieces up to as many thousands that you may need.
Submit your existing design or enlist our design team to assist you in perfecting your custom bag accessories. Bag accessories are typically made from zinc alloy or brass and then plated with your choice of shiny gold, silver, copper, bronze, or pewter, and we can offer antique versions of whatever you choose. Metal logo plates, charms, buckles, snap hooks, chain and buttons all can be customized as per your request!
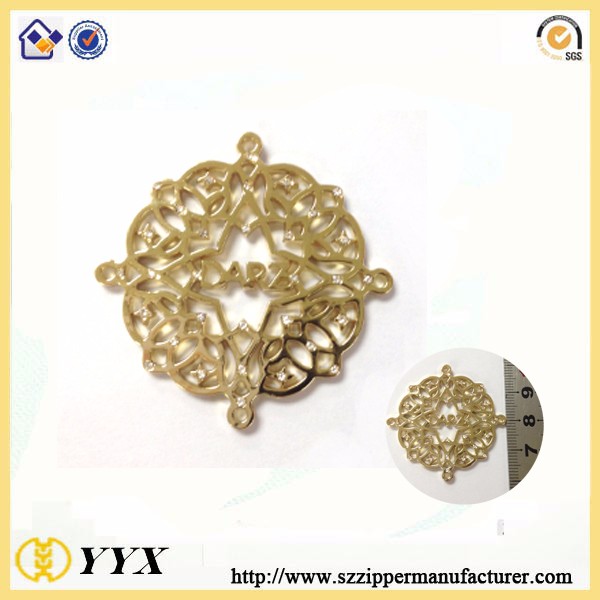
Everything looks better with YYX bag accessories.
Metal Rivets
Shenzhen Yiyixing Zipper Manufacture Co.,Ltd , https://www.yyxchina.com